In this chapter we will see various deposition techniques that are used in microelectronic fabrication. If a material like copper or tungsten has to be deposited onto the silicon wafer, there are multiple ways to achieve that goal. The deposition methods used in semiconductor industry can be divided into four groups.
- Physical Vapor Deposition (PVD)
- Chemical Vapor Deposition (CVD)
- Electrochemical Deposition (ECD)
- Spin-on coating
Among these four processes, PVD and spin-on coating are purely physical processes. CVD and ECD are chemical processes. That means in CVD and ECD, chemical reactions occur.
In IC manufacturing, the actual quantity of material to be deposited in any single step is very low. The deposited material will be in the form of a thin film, almost like the painting on a surface and in reality much thinner than the paint coating.
Thin film requirements: Any deposition method must satisfy certain requirements:
- The deposition must be uniform throughout the wafer
- A very good control is necessary. If we want 1000 nm of the material deposited on the wafer, then the variation must be within one or two percentage. i.e. the thickness of the film after deposition must be at the minimum 980 nm and at the most 1020 nm.
- In the places where trenches or vias are made, the side wall coverage must be good. This is explained in the later section (figure 3.11)
- The material should adhere to the wafer well and should not peel off
- Dust particles should not fall onto the wafer during the deposition process
- The crystal structure of the film deposited must be of sufficient quality because it will affect the properties of the film. For example, when copper is deposited, we need large grain size since it will result in less electrical resistance.
- If we are depositing alloys, then the composition must be uniform throughout the process
In general, PVD is used to deposit titanium, titanium nitrate, tantalum, tantalum nitrate, aluminum and a very thin film of copper called seed layer. CVD is used to deposit tungsten, titanium, again copper seed layer, silicon di-oxide, silicon nitride, etc. Electrochemical deposition is used for depositing copper. Spin-on coating is used to deposit insulators or dielectric materials, which are usually organic in nature.
Historically, some of the metals were evaporated and then the vapor was deposited onto the wafer. The wafer would be kept at lower temperature and the vapor will cool down and form the solid metal. This methods used large amount of energy and had other difficulties. It could not be used for all materials, and particularly for alloys. The material will also deposit on other places like the chamber walls. Hence, it is not currently used for IC manufacturing.
If the raw material is taken in gaseous form and the final material is deposited on the wafer after reaction, it is called chemical vapor deposition (CVD). If the material is taken in solid state, but sent as very small particles or atoms and deposited on the wafer without any reaction, it is called physical vapor deposition (PVD). We will first see the details of the PVD.
Physical Vapor Deposition:
DC sputtering
The PVD equipment will be about 4 ft in height and 4 ft in diameter. The material to be deposited (e.g. titanium) will be at the top, as shown in schematic Fig 3.1
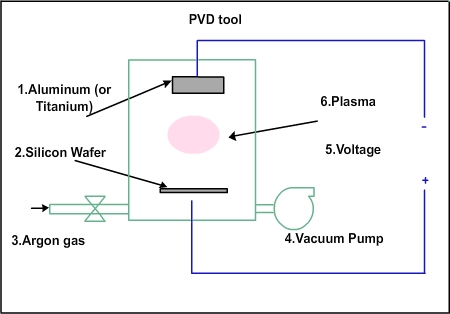
Figure 3.1. Schematic of a PVD chamber
The tungsten will be in the form of a disc of 1 inch thickness and 5 or 6 inches diameter. At the bottom, silicon wafer will be kept. Apart from these, there will be facilities to allow gases into the chamber and to evacuate the chamber with vacuum pump and electrical connections to apply very high voltage (of the order of 10000 V). The negative plate will be near the tungsten and the positive plate will be near the wafer. Tungsten (or any other material in its place) is called target. Why is it called target? How is it deposited onto the wafer?
Let us consider an example. In old houses, if we stand inside the house and throw a ball at the top of the house, some of the dust material will fall on the floor. If we throw the ball repeatedly, after some time, the whole floor will be covered with dust. Some dust particles may be coarse and may not stick well to the floor. The fine dust particles will stick well to the floor.
In PVD, we can visualize a similar process: Instead of the ball, argon ions are used. The ceiling represents the tungsten target. When the ions hit the target, a few atoms will break away from the target and fall on the wafer. This is a very simplified description of PVD process. PVD is also called sputtering.
First the air in the chamber must be removed and vacuum must be created. Then argon gas sent inside and a low pressure will be maintained. If high voltage is applied to the plates, a plasma will be generated. The plasma will have electrons and positive argon ions. The plasma cannot be generated by normal 230 volts. The positive argon ions will be attracted towards the negative plate. They will move towards the negative plates and hit the tungsten with high force. That is why tungsten is called target in this process.
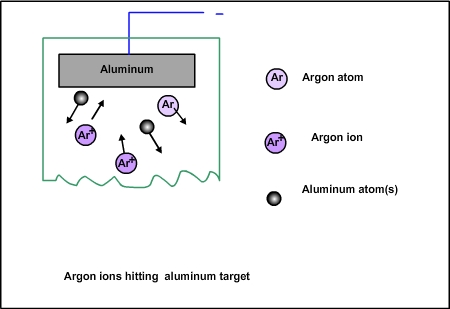
Figure 3.2. Argon ions hitting the target
Since the argon ions impinge on the target with large force, some of the target atoms will break and come out , as shown in Fig 3.2. How many tungsten atoms will come for each argon ion hitting the target? This number is called sputtering yield. It depends on the speed of the argon ions, the angle of the impact and also on the bond strength of the target. Tungsten is one of the hard materials. If a relatively soft material such as copper is used as target, then the yield will be higher.
The atoms from the target will come towards the wafer with some force. Not all of them will deposit on the wafer. Some will be deposited (Figure 3. 3), while some will bounce back (Figure 3.4). Some may even bounce back and remove some of the materials already deposited on the wafer (Figure 3.5)
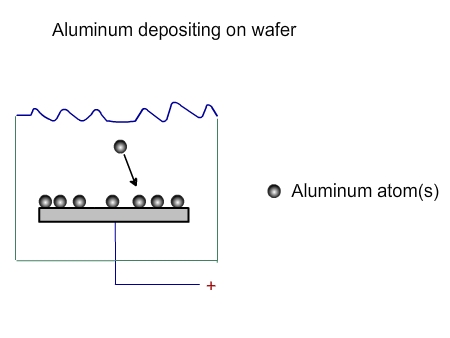
Figure 3.3. Processes near wafer in a PVD chamber. Deposition
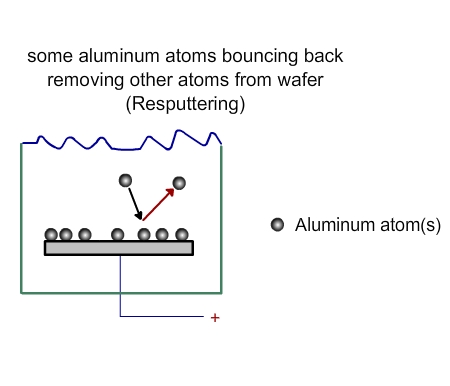
Figure 3.4 Processes near wafer in a PVD chamber. Bounce back
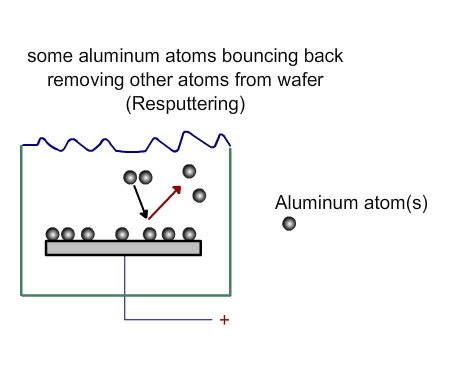
Figure 3.5 Processes near wafer in a PVD chamber. Resputtering
Among the tungsten atoms that fall on the wafer, the fraction that stick to the wafer is called sticking coefficient. If all the atoms that fall on the wafer stick to it, then the sticking coefficient is one. If none of them stick, then the sticking coefficient is zero. Typically, the sticking coefficient is about 0.7 to 0.8.
|