The production level CMP tool will be approximately 6 feet tall and 8 feet in diameter. It has a large round table which can rotate. Some variants of the tool make linear or a combination of linear and sidewise movement. On top of the table, a soft material called pad will be present. The wafer will be help upside down and pressed onto the pad. The tool has facilities to control the pressure at various points of the wafer. A slurry, which is a combination of chemicals and abrasive particles, will be made to flow between the wafer and the pad. The wafer and the table will move and the relative movement will cause removal of material. (Figure 4.10). The removal rate depends on the pressure, the speed of rotation, the concentration of chemicals in the slurry and the particle nature and size.
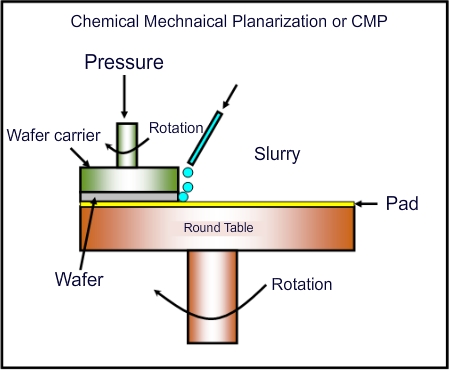
Figure 4.10. Schematic of Chemical Mechanical Polisher

Figure 4.11. Schematic of wafer at the beginning of CMP
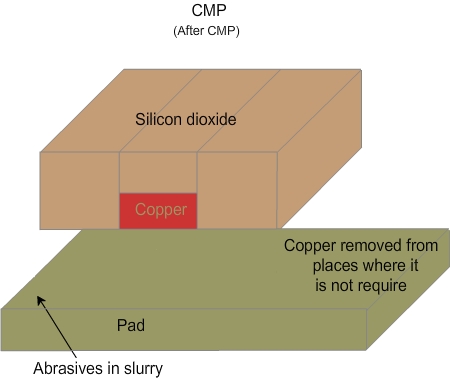
Figure 4.12. Schematic of wafer at the end of ideal CMP
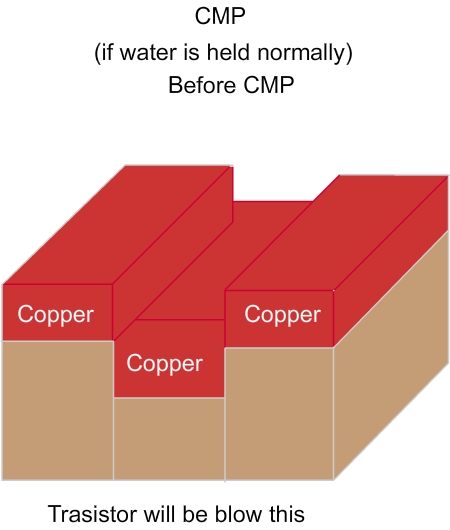
Figure 4.13. Schematic of wafer in the beginning of CMP
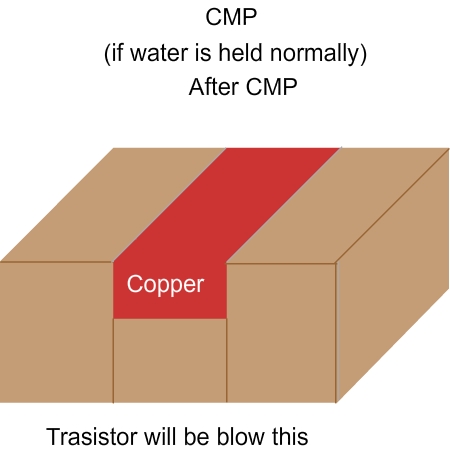
Figure 4.14. Schematic of wafer at the end of CMP
What is the role of chemical and what is the role of abrasive? The chemicals are necessary for obtaining selectivity. i.e. if one material has to be removed and another material should not be removed, the slurry should contain a suitable chemical. For example, in Fig 4.7, copper has to be removed and silicon dioxide should not be removed. For this, a chemical which dissolves copper and not silicon dioxide should be chosen. When all the copper over silicon dioxide is polished, the silicon dioxide will not be removed. The particles or abrasives are needed to obtain a planar surface. The higher levels (peaks or hills) will be removed faster while the material at the lower level (valley ) will be removed slowly. Thus the wafer will be planarized.
For example, to remove excess copper, a slurry containing nano size silicon dioxide particles (abrasives) and chemicals such as oxidizers, complexing agents and corrosion inhibitors. The pad is made of a polymer material such as poly urethane. For removal materials like silicon dioxide, a hard pad is used, while a soft pad is used for removing materials like copper. Here, the terms soft and hard are used in a relative sense. A soft pad may be similar to ‘puff’ used for applying powder to the face, while the hard pad may have a texture and feel similar to that of a leather bag.
There are two goals in CMP. One is to remove excess material and the second is to planarized the surface. When a material is deposited on wafer, it may not be deposited uniformly. CMP can be used to planarized such surfaces also.
Dishing and erosion: Two of the major issues that arise during CMP are dishing and erosion. Consider the set large copper wire shown in figure 4.15. Before planarization, the deposited copper film will look as shown in fig 4.15a. After planarization, ideally, the surface must be flat as shown in fig 4.15b. However, the pad is not a perfectly rigid and straight body and it can in fact bend slightly. Because of that, the copper will be removed as shown in fig 4.15c. This unwanted removal of copper, leading to non planar surface and high resistance wire is called dishing. This occurs especially on wide lines.
 before CMP nv.jpg)
Figure 4.15 a. Schematic of wafer (a) before CMP
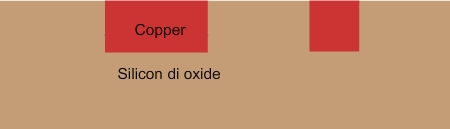
Figure 4.15 b. Schematic of wafer after CMP (ideal case)
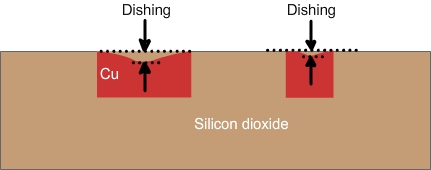
Figure 4.15 b. Schematic of wafer after CMP (real case). Note the dishing in real CMP.
|