Figure 5.3 Multiple reheat and intercool cycle |
The cycle tends towards the Ericsson cycle, the efficiency is same as that of the Carnot cycle
The use of intercoolers is seldom contemplated in practice because they are bulky and need large quantities of cooling water. The main advantage of the gas turbine, that it is compact and self-contained, is then lost.
Actual Gas Turbine Cycle
Efficiency of the compression and expansion processes will come into consideration.
Pressure losses in the ducting, combustion and heat exchanger.
Complete heat exchange in the regenerator is not possible.
Mechanical losses due to bearings auxiliary etc are present.
Specific heat of the working fluid varies with temperature.
Mass flow throughout the cycle is not constant.
Gas Turbine Cycles for Propulsion
In aircraft gas turbine cycles, the useful power output is in the form of thrust. In case of turbojet and turbofan (Figure 4.1), the whole thrust is generated in the propelling nozzel, whereas with the turboprop most is produced by a propeller with only a small contribution from the exhaust nozzle. A turboprop and a turbojet engine is illustrated in Figure 5.4and 5.5 respectively.
(i) Turboprop
Figure 5.4 Turboprop Engine |
Power must eventually be delivered to the aircraft in the form of thrust power, just as it is with a piston engine driving a propeller. The thrust power ( TP ) can be expressed in terms of shaft power ( SP ), propeller efficiency ( ) and jet thrust F by
where
is the forward speed of the aircraft . (ii) Turbjet Engine
Figure 5.5 Turbojet Engine |
Figure 5.6 Propelling Nozzle |
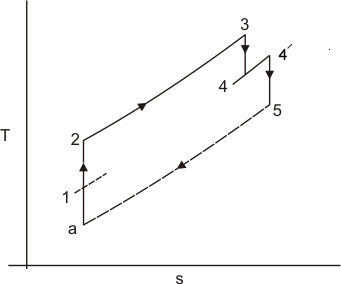
Figure 5.7 Turbojet Cycle
|
a-1 -> ram effect in intake.
1-2 -> isentropic compressor
2-3 -> constant pressure heat addition in the combustion chamber
3-4 -> Isentropic expansion in the turbine
4- ->Constant pressure heat addition in the after burner
-5 -> isentropic expansion in the nozzle
|
Propelling nozzle refers to the component in which the working fluid is expanded to give a high velocity jet. Between the turbine exit and propelling nozzle, there may be a jet pipe. When thrust boosting is required, an afterburner may be introduced in the jet pipe as shown in figure 5.7. Figure 5.7 indicates the ideal turbojet cycle on the T-S diagram, which is often used to evaluate the design performance of a turbojet engine.
After reviewing the thermodynamic cycle for a gas turbine or aircraft engine, characteristic features and performance of individual components such as the compressor, turbine, combustion chamber and nozzle (in case of aircraft engine) will be discussed in the following section. |