|
contd...
Table 5.1 |
Key characteristics of Ceramic Monoliths, Square Cells |
Parameter |
Ceramic Cell Density , cells per in2 / wall thickness,10-3 in
(cells per cm2 / wall thickness , mm)
|
|
400/6.5
(62/0.17)
|
600/4
(93/0.10) |
900/2.5
(140/0.064) |
Substrate diameter, mm |
105.7 |
105.7 |
105.7 |
Substrate length, mm |
98 |
76 |
76 |
Substrate volume, l |
0.86 |
0.67 |
0.67 |
GSA, m2/ l |
2.74 |
3.48 |
4.37 |
OFA, % |
75.7 |
81.4 |
85.6 |
Rf , litres/cm2 |
3074 |
3990 |
5412 |
Substrate mass, g |
339 |
202 |
156 |
Metal Monoliths
Metallic monoliths as an alternative to ceramic were introduced to provide high mechanical strength.. In metallic monoliths, alternate flat and corrugated thin foils of made of high temperature and corrosion resistant steel containing aluminium, are wound in a spiral shape to form the honeycomb structure. The foils are about 0.05 mm thick and even thinner foils down to 0.02 mm thickness are now used. The honeycomb structure is fixed in an outer metal shell called as mantle.. Front view of a metallic monolith substrate is compared with ceramic monolith in Fig 5.11.
The size of corrugations in the corrugated foil is designed to obtain the required cell geometry and cell density. Various geometries of corrugations and hence the varying
designs of cell structure are used to enhance turbulence. The coiled foils are coated with a special brazing material and brazing joins the coil with housing so that it functions as a single unit. The washcoat is applied to these monoliths mostly after their fabrication into final shape.
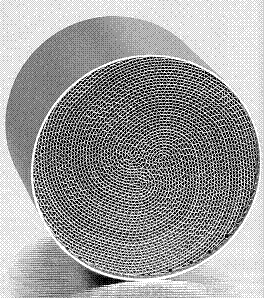 |
Frontal View of Metallic Monolith |
Ceramic Monolith Cells |
Metallic Monolith Cells |
Figure 5.11 |
Frontal view of a metal monolith and comparison of cell formation in ceramic and metallic monoliths |
The foil thickness of a metallic monolith of 400-cpsi is typically 0. 0.04 to 0.05 mm compared to 0.15 to 0.20 mm for an early 400-cpsi ceramic monolith. A comparison of flow and physical characteristics of ceramic and metal monoliths is given in Table 5.2. The metallic monoliths in general, have 20 to 30% higher GSA and 10 to 20 % higher OFA. The mass of metallic monolith is however, about 2 times higher than the ceramic monolith of the same volume and cell density. The thermal capacity of metallic monoliths is 15 to 80% higher than the comparable ceramic monoliths. The metallic monoliths however, have 10 to 15% lower backpressure. A disadvantage with metal monoliths is that these cool down faster at lower loads and have to be fitted as close to the engine as possible taking into account the peak temperatures that might occur. The metallic support is non-porous and special techniques to obtain adherence of wash coat and hence catalyst on the surface have to be employed.
|