Palletized Catalysts
The first catalytic converters introduced in 1970s and used until early 1980s employed spherical ceramic pellets, which were packed in a catalyst bed. The pellets of 3 to 6 mm dia were made of γ- alumina (Al2O3) The porous surface of alumina pellets provides a large surface area on which the noble metal salts are impregnated to a depth of about 250 μm. The pellet catalysts are loaded with approximately 0.05% by weight of noble metals. A typical pellet type catalytic converter is shown in Fig 5.10.
The gas flow through the packed bed pellet reactors is a mix of axial and radial flow so as to provide large flow area and reduce flow resistance. The gas flow through pellet bed is turbulent resulting in high mass-transfer rates. The packed bed catalysts suffer from the following disadvantages:
- High pressure drop
- Are heavy, have high thermal inertia and hence slow to warm-up.
- Loss of catalyst from abrasion due to rubbing of pellets against each other.
Therefore during 1980s the ceramic honeycomb or metallic matrix monolith converters replaced the pellet type converters.
Figure 5.10 |
Pellet type catalytic converter. |
Ceramic Monoliths
A ceramic monolith is shown schematically in Fig 5.11. It has parallel flow channels or cells of square or triangular cross section. The flow through these channels is laminar. The ceramic material commonly used is porous cordierite (2MgO. 2Al2O3.5SiO2). The monoliths are characterized by cell density (cells /in2 or cells/cm2 of monolith cross section area) and wall thickness of the cells. A typical substrates used during 1980s and 1990s had 400 cpsi (cells /in2) and a wall thickness of 6x10-3 inch (0.15 mm), and it is designated as 400/6.The unit cpsi used is cells /in2 of cross section area of monolith ( 1 cpsi = 6.45 cells /cm2 ) . In the current vehicles, the ceramic substrates of 600/4 configurations are quite common. The 900/2.5 and 1200/2 substrates are also being used for special catalytic converters such as closed-coupled catalysts for cold start and warm-up emission control. With increase in cell density, geometric surface area (GSA) increases providing more catalyst activity for the same volume of substrate. However, at higher cell density the cell dimensions get smaller and flow resistance (Rf) increases. Open front area of the substrate is expressed as percent of cross sectional area perpendicular to the flow direction and represents actual flow area for gases. Some important characteristics of ceramic monoliths of different structures are given in Table 5.1. Due to high surface area, the high cell density substrates provide overall higher emission .reductions.
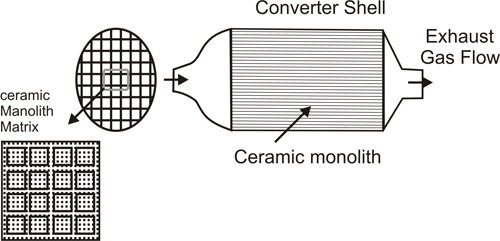 |
Figure 5.11 |
Ceramic monolith catalyst substrate having square cells. |
|