The solution is given by . Here, t is the time corresponding to ‘creating the initial oxide from bare silicon’ and is given
by , with . The solution can also be written as .
Note that the values of “A” and “B” depend on the diffusivity and the value of ‘n’. Thus, they are different for wet and dry oxidation. They also vary with temperature.
At short time intervals and at long time intervals . Hence, at the short time interval, if we start with the pure silicon, the growth rate of oxide will be in what is known as linear regime. At longer time intervals the growth rate will be slower because the oxidation species has to diffuse through an already existing thickness of oxide, and it will be slower and it is called parabolic regime. In the beginning the growth rate is controlled by the maximum reaction possible (i.e. the kinetic controlled reaction). At later stage, a thick oxide will have formed and the transfer of the species or the diffusion of the species will limit the growth rate. This is called mass transfer controlled growth. The overall implication is that thicker oxide needs more time to grow than thinner oxide. The entire model describing this phenomenon is called Deal-Grove model which was first proposed by Bruce Deal and Andrew Grove. (Andrew Grove was the one of the founders of the Intel Corporation, USA).
Variation of rate constants with temperature: The values of D and k (and hence A and B) will depend on the operating temperature. The linear and parabolic rate constants are exponentially related to the temperature as shown in the figures. Note that constants are more for wet oxidation compared to dry oxidation. Typical oxidation temperature range is between 900 and 1200 ◦C.
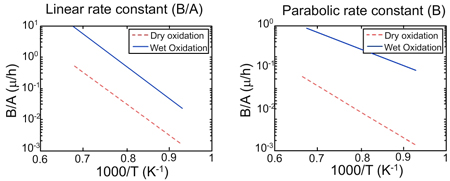
Fig 7.3. Arrhenius plot of linear and parabolic rate constants, for wet and dry oxidation .
The plots are given for Si(100) and will change for other crystal orientations. The growth rate will also depend on the dopant level and are not considered here.
Dopant redistribution: We should note that the solubility of the species also plays an important role in deciding the growth rate. For example the solubility of stream in oxide is much more than the solubility of dry oxygen and hence the growth rate is more in the wet oxidation. There are two reasons why the growth rate is more in wet oxidation. One is that the solubility of stream is more; the second is the oxide formed is porous allowing easy diffusion of the species. Few other parameters also affect the oxidation kinetics. If the silicon is doped then the doping usually increases the oxidation rate, because it will increase the diffusivity. Second the dopant will redistribute silicon and silicon dioxide. This is called segregation. The ratio of dopant in silicon and silicon dioxide is usually not one, hence after oxidation some dopant will either move into the silicon dioxide or it will move away from silicon dioxide and into the silicon. This depends on the nature of the dopant. For example if boron was originally present, if it was a P-type silicon with boron as the dopant then it will redistribute itself and will be incorporated in the oxide, it will enhance the diffusion and the parabolic rate constant will be higher. If phosphorous is present it will not be incorporated into the oxide, and it will not cause significant change in the parabolic rate constant.
Exponential growth regime: If we start with bare silicon (i.e. silicon with only native oxide) then we find that the value of t is not zero (or 2 nm) in the model fit. Instead, a value of about 25 nm provides a good fit. This indicates that the initial growth is very rapid. This growth is approximated by an exponential curve. This is also called exponential growth regime. Different hypotheses have been proposed to explain this observation. In one hypothesis, the holes diffuse faster and setup an electric field. Due to this, the net diffusivity of the oxidizing species is higher. This space-charge regime is about 15 nm thick for dry oxidation and 0.5 nm thick for wet oxidation. Hence, the effect is observed in dry oxidation but not in wet oxidation. In another hypothesis, even before oxidation starts (i.e. temperature is raised), oxygen diffuses into the silicon. Once the temperature is increased, oxidation occurs simultaneously throughout the depth (of 5 or 10 nm) and hence initial oxide growth rate is high. In any case, the fact is that initial growth rate of oxide , in dry oxidation, is much higher than that predicted by Deal-Grove model.
Furnaces: The oxidation is conducted in high temperature furnaces. The furnaces may be either vertical or horizontal tube furnaces. In one batch many wafers (~100) will be processed. The duration of the process, the supply of gas and the heating are precisely controlled using computer. In horizontal furnaces, contamination can be an issue and vertical tube furnaces were introduced to minimize this issue. At present, wafers of 300 mm diameter are commonly used in the industry. In the vertical tube furnaces, the wafers are loaded from the top, in cassettes (batch of 10 or 13 wafers). In horizontal furnaces, the movement of the cassette against the furnace wall will generate particles, and this is avoided in the vertical furnaces. Also, since the gas moves vertically, there is no separation of gas due to density difference. In horizontal tube furnace, the gas will flow in the horizontal direction, which leads to lighter gases moving up. This results in uneven distribution of gases and hence lack of uniformity in the oxide grown. In vertical furnaces, better uniformity can be achieved.
High pressure oxidation: One of the problems with the high temperatures used in oxidation process is that the dopants already present in the wafer will diffuse. Besides defects such as dislocations are also likely to be more at higher temperatures. However, if oxidation is done at higher pressure (i.e. higher concentration), then the same growth rate may be obtained at lower temperature and/or time. If the pressure is increased to about 25 atm, then the temperature can be reduced by 300 to 750 ◦C.
Electrochemical oxidation: Electro chemical oxidation is a process in which silicon is kept in a solution usually water or alcohol, with few other chemicals and another electrode is kept in the same solution. Silicon will be connected to the positive terminal of a battery and the other electrode will be usually platinum electrode and that will be connected to the negative terminal. When this voltage or potential is applied oxygen will form at the silicon electrode and it will react. This will form silicon dioxide and this method is sometimes referred to as anodic oxidation. Usually the silicon dioxide that’s formed here will be very porous and it is of poor quality as far as microelectronic fabrication is considered. However the pore structure and the pore length can be controlled by changing the chemicals as well as the potential and a porous oxide is frequently found useful micro electro mechanical systems that are MEMS and hence the electro chemical oxidation is frequently used in the formation of porous silicon in the MEMS. As far as the semiconductor processing is concerned the chip fabrication, dry oxidation and wet oxidation are the major processes used for oxidizing the silicon.
|