Example
A cantilever aluminium beam of length 150mm is fully covered by a viscoelastic material ISD112 from 3M, and an aluminium constraining foil (Table 39.1). The geometric properties of the beam and the ACLD system are given in Table 39.2. A piezoelectric patch actuator is working over the active layer and is partly covering the top layer from 20 to 50mm. Find out the effect of the CLD and the PZT actuator on the loss-factor.
Table 39.2: Geometric details of the beam
Component |
Material |
Coverage (mm) |
Cross Section (sq. mm) |
Beam |
Aluminium |
0-150 |
38 × 3.175 |
 |
|
|
|
Viscoelastic Layer |
ISD112 |
0-150 |
38 × 0.127 |
 |
|
|
|
Cons. Layer |
Aluminium |
0-150 |
38 × 0.254 |
 |
|
|
|
PZT actuator |
Sonox P5 |
20-50 |
30 × 0.400 |
|
Table 39.2
Solution
Following eqn. 39.2) and using Table 39.1 and 39.2, one can obtain the governing equation of motion. Using MATLAB, this equation of motion is solved for eigenvalue analysis and the frequency and loss-factors are obtained for the first eight modes. The results are plotted in Fig. 39.1.
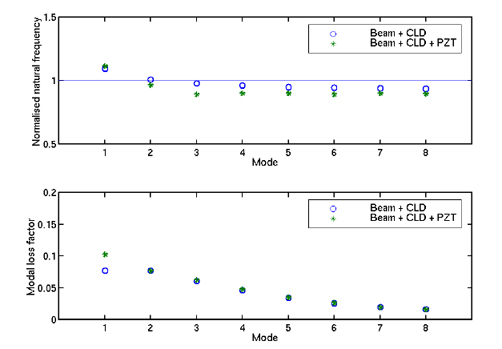
Figure 39.1: Natural frequency and modal loss factor for different modes
Figure 39.1 shows the effect of adding CLD and PZT layers on the natural frequencies and modal loss factors. The natural frequencies are presented as a fraction of the natural frequency of the plain beam. It can be seen that the addition of PZT layer has caused increase in the fundamental frequency but has reduced the frequencies corresponding to the higher modes. It can also be observed that that the loss factors are better for the first two modes and then it decreases for the higher modes. In fact, by choosing the active layer coverage intelligently one can achieve more damping for the higher modes. For passive damping the added stiffness of the PZT only significantly affects the first mode.
Congratulations! You have finished Lecture 39. |