Washcoat Monolithic substrates have a geometrical surface area of 2.0 - 4.0 m2/l of its volume. This is too low to provide high contact area between the catalyst and reacting gases for high conversion rates. A thin layer of γ-Al2O3 seeded with other oxides as ‘washcoat’ is
applied to the monolith cells to increase effective surface area for dispersion of catalyst material. About 20 percent of other oxides consisting of cerium oxide (CeO2) and stabilizers such as zirconium oxide and barium oxide are added to alumina. The washcoat has pores of varying sizes ranging from 0.2 to 1 μm. The ceramic monolith walls are porous and surface is rough so that good adhesion of washcoat is obtained.
High surface area created by Al2O3 washcoat and dispersion of active catalyst deposited by solution impregnation is shown schematically in Fig. 5.12. Adhesion of washcoat to metallic monoliths requires at first pre-treatment of surface to make it rough and improve its bonding characteristics with ceramic washcoat materials. For the prefabricated metallic monoliths then, a procedure similar that for the ceramic monoliths may be followed.
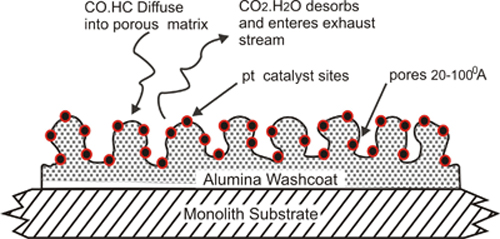 |
Figure 5.12 |
Conceptual model of catalytic sites dispersed on a high surface-area Al2O3 washcoat. |
The washcoat constitutes 5 to 15 percent of the mass of ceramic monoliths. Its thickness typically varies in the range 10-30 μm on the walls. The washcoat increases actual surface area of the catalyst substrate to 10000-40000 m2/l of monolith volume. are added.
Converter Housing
The ceramic monolith is mounted in a metal casing made of high quality corrosion resistant steel. A mat made of ceramic material around the ceramic monolith holds it tightly inside the casing. The mat protects the ceramic monolith against mechanical impact and vibrations, and also acts as heat insulation. The ceramic mat is made of aluminium silicate that expands as it is heated.
As the temperature of mat rises, gas bubbles are formed inside the mat and it ensures proper tightening of the ceramic monolith in the housing and sealing to prevent any bypass of the exhaust gases. The metallic monolith converters are easier to mount as the metal mantle that holds the metallic honeycomb structure is welded or brazed in the exhaust system of the engine.
|