Natural |
|
Synthetic/Man made |
 |
Polyester |
 |
Nylon |
 |
Acrylic |
 |
Viscose |
|
Constituent |
Composition of a fibre |
|
Typical (%) |
Low (%) |
High (%) |
Cellulose hyperlink11 |
94.0 |
88.0 |
96.0 |
Protein hyperlink12 |
1.3 |
1.1 |
1.9 |
Pectic matter hyperlink13 |
0.9 |
0.7 |
1.2 |
Wax hyperlink14 |
0.6 |
0.4 |
1.0 |
Mineral matter hyperlink15 |
1.2 |
0.7 |
1.6 |
Organic acids hyperlink16 |
0.8 |
0.5 |
1.0 |
Total sugars hyperlink17 |
0.3 |
- |
- |
|
References |
- Hardin I.R. & Li Y., Textile Chemists & Colorists, 29 (8), 1997, 71.
- Hardin I.R., Kim J., Colourage, 2000, 43.
- Takagishi T., Yamamoto R., Kikuvama K., Arakawa H., AATCC Review, August 2001, 32.
|
Most of the impurities in cotton are concentrated in the primary cell wall. |
Chemical structure of cellulose - hyperlink4/ hyperlink11 |
Physical Structure of cotton fibre - hyperlink5 |
Hyperlink5
|
|
Microscopic view of cotton |
|
Layered physical structure of cotton |
|
hyperlink12 |
Proteins |
- Nitrogenous compounds
- Present in primary cell wall and lumen
- Yellow colour of cotton is due to presence of proteins and some colouring matter
|
Some amino acids:
|
Leucine |
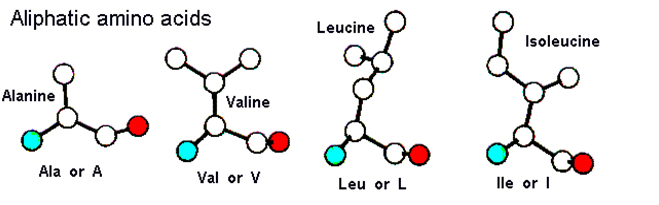 |
Valine |
Proline |
Alanine |
|
hyperlink13 |
Pectins |
- Derivatives of pectic acid
- Found in the cover of citrus fruits
- Polymer of high molecular weight
|
Pectin is a polysaccharide that acts as a cementing material in the cell walls of all plant tissues. It is a polymer of α-Galacturonic acid with a variable number of methyl ester groups |
Some COOH groups are present as Ca and Mg salts. |
|
hyperlink14 |
The wax present in the primary cell wall of cotton protects the fibre from environmental agencies, is responsible for the smooth handle and is a source of hydrophobicity. In the presence of wax, cotton has poor wettability. The wax consists of long chains of fatty alcohols, fatty acids, their esters, cholesterin & hydrocarbons. |
Components of fats and waxes |
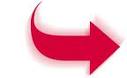 |
Fatty acids |
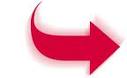 |
Stearic acid |
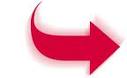 |
Palmitic acid |
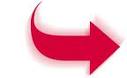 |
Oleic acid |
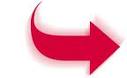 |
Fatty alcohols |
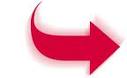 |
Gossipyl alcohol (C30H61OH) |
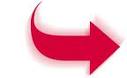 |
Cetyl alcohol (C26H53OH) |
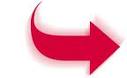 |
Montanyl alcohol (C28H57OH) |
|
hyperlink15 |
Mineral matter (Ash) consists mainly of alkaline earth compounds and potassium and phosphate ions. The mineral matter may be water soluble or may be removed by treatment with dilute mineral acids (demineralization/souring). Composition of mineral matter on a fibre Depends on soil composition. |
Composition of mineral matter for a typical cotton fibre:
|
Mineral |
% fraction |
Potassium carbonate |
44.8 |
Potassium Chloride |
9.9 |
Potassium sulphate |
9.3 |
Calcium sulphate |
9.0 |
Calcium carbonate |
10.3 |
Magnesium sulphate |
8.4 |
Ferric oxide |
3.0 |
Aluminum oxide |
5.0 |
|
hyperlink16 |
Colouring Matter |
Colored pigments present are |
|
3,5,7,2’,4’ penta hydroxy flavone (Morrin) (gossypetin) |
|
3,5,8,3’,4’ Hexa hydroxy flavone |
|
Hyperlink2 |
Wool is a protein fibre |
Impurities in wool |
Type |
Fat and suint |
Sand an dirt |
Vegetable matter |
Wool |
Fine |
20-25 |
5-40 |
0.5-2 |
20-50 |
Medium |
15-30 |
5-20 |
1.5 |
40-60 |
long |
5-15 |
5-10 |
0.2 |
60-80 |
|
As is clear from the above table, finer wools tend to have a higher proportion of impurities as compared to coarser wool.
|
Impurities: |
Wool wax (Fat) –Easily saponifiable and emulsifiable hydrophobic impurity It consists of:
|
- Esters
- Diesters
- Hydroxy esters of high M. Wt Lanolin alcohol and acids
|
Suint |
It is the perspiration of sheep and is generally water soluble/insoluble. |
Sand and dirt |
Particulate type of impurity which sheep picks up during its movement. |
Vegetable matter |
Parts of dried leaves and some sticky seeds of certain plants. These are primarily cellulosic in nature. |
Hyperlink3 |
Silk is a minor fibre in terms of volume produced (~1% of world fibre production) but is a high value fibre. |
Composition of a typical silk fibre |
Element |
% |
Fibroin |
70-80 |
Sericin |
20-30 |
Waxy matter |
0.4-0.8 |
Inorganic matter |
1.2-1.6 |
Pigment |
0.7 |
|
The major impurity in a silk fibre is sericin. Both Fibroin, which form the actual silk fibre and the sericin are proteins. Hence some of the approaches for removal of sericin may result in some damage to silk (fibroin) also.
|
|
|