1.1 Introduction, Classification and Developments (2 Lectures)
|
This chapter introduces the high-performance fibres and speciality fibres. The classification and developments of these fibres are briefly discussed. |
How are High-Performance and Speciality Fibres different from commodity fibres ? |
Commodity fibres or general purpose fibres are typically used in a highly competitive price environment which translates into large scale high volume programs in order to compensate for the (often) low margins.
|
Conversely, high performance and speciality fibres are driven by special technical functions that require specific performance properties unique to these fibres. |
|
High-Performance Fibres are generally characterized by remarkably high :
|
-
Tensile strength and modulus
-
Resistance to heat and flame
-
Resistance to chemical agents that normally degrade conventional fibres.
|
Most high-performance fibres have high tensile modulus and strength. Many of them are also known for their thermal resistance; they do not catch fire and provide protection against heat. Therefore, fabrics constructed from these fibres can be used for applications where protection against fire is required.
|
Similarly, for certain applications, resistance against chemicals is desired. |
Speciality Fibres: These fibres have selected performance properties such as
|
|
These can be obtained by using different approaches such as : |
Using Additives such as colorants, flame retardants, conducting fillers, antistatic compounds, etc. during the spinning process. |
Surface Modification using chemical finishes for specific properties, such as hydrophilicity, high absorbency, low friction, etc. or by plasma modification.
|
Special Spinning Processes are used to produce different cross-section, bicomponent, micro, nanofibres.
|
Bicomponent fibres are "co-extruded" with two different polymers in the cross section. This allows the fibre to use the properties of both materials, and vastly expands the array of possible fibre performance characteristics. |
A non-circular cross-section can provide added functionality, such as unique lusture or moisture transport.
|
The nanofibres have a very high surface to volume ratio and find potential applications in tissue engineering, optoelectronic applications, protective textiles and next generation filters.
|
Advanced or Special Polymeric Materials are used for making smart or responsive
fibres. These can be shape changing fibres (responsive to pH, temperature or electric field), fibres that can store heat or chemicals and self adaptive fibres( i.e. self tightening sutures, self-fitting shoes and medical devices).
|
Need?
|
These are required for meeting the ever increasing applications for fibrous material in non-conventional sectors such as |
- protective clothing
- medical devices
- health care products
- automotive components
- building material
- geotextiles
- agricultural devices
- sportswear
- leisurewear
- filter media
- environmental protection
|
Strong demands on good performance properties -such as strength/modulus, durability and dimensional stability and on functions such as flame-retardancy, hydrophilicity, hydrophobicity, biocompatibility, smart and responsive textiles, sensors, etc. Figure 1 shows the applications of high performance and speciality fibres for different end-uses. |
|
Mooring & towing |
|
Gloves |
|
Trilobal fibre: for high lusture |
|
Nanofibre: with high surface to volume ratio
|
|
Figure 1. Applications of High Performance Fibres |
Classification of High Performance Fibres
|
i) Based on the performance properties: |
These are generally characterized by remarkably high values of: |
- Tensile strength and modulus
- Resistance to heat, flame
- Resistance to chemical agents that normally degrade conventional fibres
|
|
Figure 2. The step change in strength and stiffness from first generation to second generation manufactured fibres and pointer showing different generations of textile fibres
|
As shown in Figure 2 , the naturally available fibres, such as cotton, wool and silk have tenacities in the range of 0.1-0.4 N/tex and initial moduli from 2 to 5 N/tex. In earlier days, silk filament was mostly used for the demanding applications such as parachute fabric. However, with the introduction of manufactured fibres, superior strength and modulus are achieved. The reinforcement in automobile tyres moved from cotton cords in 1900, to a sequence of improved rayons from 1935 to 1955, and then to nylon, polyester and steel, which dominate the market now. A similar replacement of natural and regenerated fibres by synthetic fibres occurred in most technical textiles. The maximum strength and moduli of nylon and polyester fibres approaches 10 g/den ( ~1 N/tex) or 1 GPa and 3-10 GPa respectively with breaking extensions exceeding 10%. The moderate strength along with moderate extension in these fibres result in high work of rupture, while the good recovery properties help in withstanding repeated high-energy shocks. These are called First Generation Textile Materials. |
In 1961, DuPont researchers spun para-aramid fibres from liquid-crystal solutions. High orientation led to tenacities of 2 N/tex and moduli of 80 N/tex. Other polymer fibres have now reached tenacities over 3.5 N/tex and moduli over 150 N/tex. At the Royal Aircraft Establishment (RAE) in UK, Watt and his colleagues produced the first high-strength carbon fibres by high-temperature processing of acrylic fibres under tension. This resulted in tenacities up to over 5 GPa (3 N/tex) and moduli over 800 GPa (400 N/tex). The other group of high-performance fibres are the inorganic fibres e.g. glass fibre. Strengths of glass fibres reach 4 GPa (1.6 N/tex) and moduli 90 GPa (35 N/tex), which, on a weight basis, are less than those of aramids. These fibres are classified as Second Generation Textile Materials. These include - Kevlar, Nomex, Carbon, HPPE fibres. The Second Generation Textile fibres showed a step increase in strength and stiffness. Besides there are sevaral fibre forming materials with high thermal and chemical resistance.
|
But it must be noted that before the discovery of second generation fibres, some of the natural fibres and manufactured fibres were used for technical textile applications. |
Now there is a Third Generation of Fibres called SMART FIBRES with some special physical or chemical properties, which give a new dimension to the use of textiles. A typical example is Softswitch–fibres that become electrically conducting under pressure, or fibres that change shape with external stimuli as shown in Figure 3. Such materials can be used for artificial muscles, sensors and actuators etc. |
|
Figure 3. Animation showing stimuli sensitive fibre |
|
ii)Based on the nature of bonding: |
Based upon the nature of bonding, these can be divided into three main categories: |
The high performance fibres possess a strong and continuous axial bonding.
|
Linear polymers : These polymers belonging to this group are one-dimensional and have a very high aspect ratio. Aramids, gel-spun PE, thermotropic polyesters, PBO etc. are the part of this category. Ultra high molecular weight polyethylene with linear string of covalently linked carbon atoms and hydrogen bonds in the transverse direction is a simplest case of this class. While the other polymers such as Kevlar and rigid rod polymers have a more complicated transverse structure containing aromatic rings and side groups. As shown below, the attempt is to obtain an ideal extended chain conformation of linear polymers with reduced/no defects in the structure. Theoretical moduli of ~100 GPa were calculated in the direction of primary bonds, but only ~0.5 GPa when controlled by Vander Waals bonds.
|
|
Figure 4. Ideal extended chain structure |
|
Innovations were required to achieve such fully extended ideal structures. Two extreme of molecular characteristics were employed to achieve the necessary structure. The two routes used are: |
- Using rigid and interactive polymer chains
- Using flexible and inert polymer chains
|
During processing, the rigid chains tend to associate as blocks of parallel chains or liquid crystals. The polymer molecules are fully extended because the folding is difficult due to the rigidity of the chain. The deformation of such a system during solidification would result in highly oriented structure. The chemical structure of some rigid polymers suitable for producing high performance fibres are shown in Figure 5.
|
|
|
|
Figure 5. Chemical structures of rigid polymers |
|
The alternate route of production of HM-HT fibres is based on the ease with which flexible, inert chain-molecules can be pulled out into a fully-extended, oriented state. At molecular level, this has been achieved by spinning of ultrahigh molecular weight polyethylene in the gel form and super drawing of the extruded filament in the gel form to result in an highly extended structure. As shown in Figure 6 these fibres have strong covalent bonds in the axial direction of fibre and weak intermolecular bonding in transverse direction.
|
|
Figure 6. Strong axial covalent bonds and weak transverse intermolecular bonding |
Two-Dimensional Graphitic Sheets : Two dimensional molecular sheets or structures can be obtained only by a specific geometry for the bond directions for example: hexagonal planar network of carbon can result in graphite structure. The high temperature controlled oxidation and carbonization of organic fibres under tension can be used to obtain strong and stiff carbon fibres with axial orientation of graphitic sheets (Figure 7).
|
|
Figure 7. 2-Dimensional Graphitic Sheets of Carbon Fibre |
|
Three-Dimensional Networks : Trifunctional or multifunctional precursors/monomers can be used to derive three-dimensional (3D) networks (Figure 8). Such networks in the fibre form are the basis of thermoset, glass and ceramic fibres.
|
|
|
b) |
Figure 8. 3D- Network materials: (a) A crystalline network in a ceramic fibre; (b) An amorphous network as in glass. |
|
Generally, these polymeric fibres have strength, stiffness and breaking extensions comparable to conventional textile fibres. Strong intermolecular bonding gives thermal resistance and the inert molecular structure impart chemical resistance in these fibres. The three-dimensional inorganic networks, such as those constituting ceramic and glass fibre also possess high thermal resistance.
|
High performance fibres can be used for reinforcement of composites to enhance their performance properties. The following example can illustrate how the uniaxially oriented glass fibre in polyester resin can enhance the modulus by nearly 10 times. |
Glass fibre reinforced polyester composite:
|
Example: Uniaxially oriented glass fibre in polyester resin as shown in Figure 9 below. |
The reinforced composite prepared using |
40% Glass fibres (Vg)
60% Polyester resin (Vr) |
Modulus of glass fibre (Eg) = 69 GPa, |
Modulus of polyester resin used for the matrix ( Em) = 3.4 GPa |
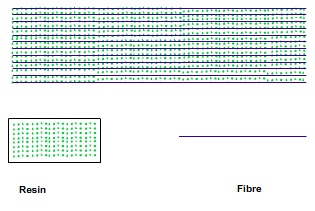 |
Figure 9. Schematic of unidirectional glass fibre reinforced composite |
|
|
Longitudinal modulus of elasticity = 69 x 0.4+ 3.4 x 0.6 = 30 GPa
|
Fibre load (Ff) / Matrix load (Fm) = σg .Ag / σr .Ar
|
= Ef. Vf / Em . Vm =69x 0.4 / 3.4 x 0.6 or Ff / Fm = 13.5 |
|