A nonwoven is a sheet of fibres, continuous filaments, or chopped yarns of any nature or origin, that have been formed into a web by any means, and bonded together by any means, with the exception of weaving or knitting. Felts obtained by wet milling are not nonwovens. (www.edana.org) |
Nonwovens are engineered flat structured sheets which are not made by weaving or knitting but by bonding and entangling fibres by means of mechanical, thermal or chemical processes. Nonwoven technology has attracted the attention of the researchers and industrialists as it can manufacture the fabric at a very high production rate bypassing the yarn production stage. The principal end uses of nonwoven materials are in the domain of Technical Textiles such as geotextiles, filtration, wipes, health and hygiene products, surgical gowns, face masks, automotive textiles etc. The two major stages of nonwoven manufacturing are web formation and web bonding. The major nonwoven technologies now available can be listed as shown below: |
Web formation |
Web bonding |
Mechanically formed fibre webs (Drylaid) |
Needlepunching |
Aerodynamically formed fibre webs (Drylaid) |
Hydroentanglement |
Hydrodynamically formed fibre webs (Wetlaid) |
Thermal bonding |
Polymer-laid (Spunmelt nonwovens) |
Chemical bonding |
|
Drylaid, wetlaid and polymer-laid web formation systems have their roots in textile, paper making and polymer extrusion processes.
|
Needlepunching Technology
|
Needlepunching is the most common web bonding method. It is the method of consolidation of fibrous webs by the repeated insertion of barbed needles into the web as shown in Figure 1.21. The needling can be done either from one side or from both (top and bottom) sides of the web. This process consolidates the structure of fibrous web without any binder by interlocking of fibres in the third or ‘Z’ dimension. Continuous filaments or short staple fibres are initially arranged in the form of a fibrous web in various orientations (random, cross, parallel, or composite). This forms a three-dimensional intermingled structure which fulfils the necessary requirements of geotextiles.
|
Needlepunched nonwoven geotextiles are extensively used in civil engineering applications including road and railway construction, landfills, land reclamation and slope stabilization. Such applications require geotextiles to perform more than one function including filtration, drainage, and separation. The properties of needle-punched nonwoven depend on parameters like fibre type, web aerial density, needle penetration depth, punch density (number of punches/cm2) and number of needling passages.
|
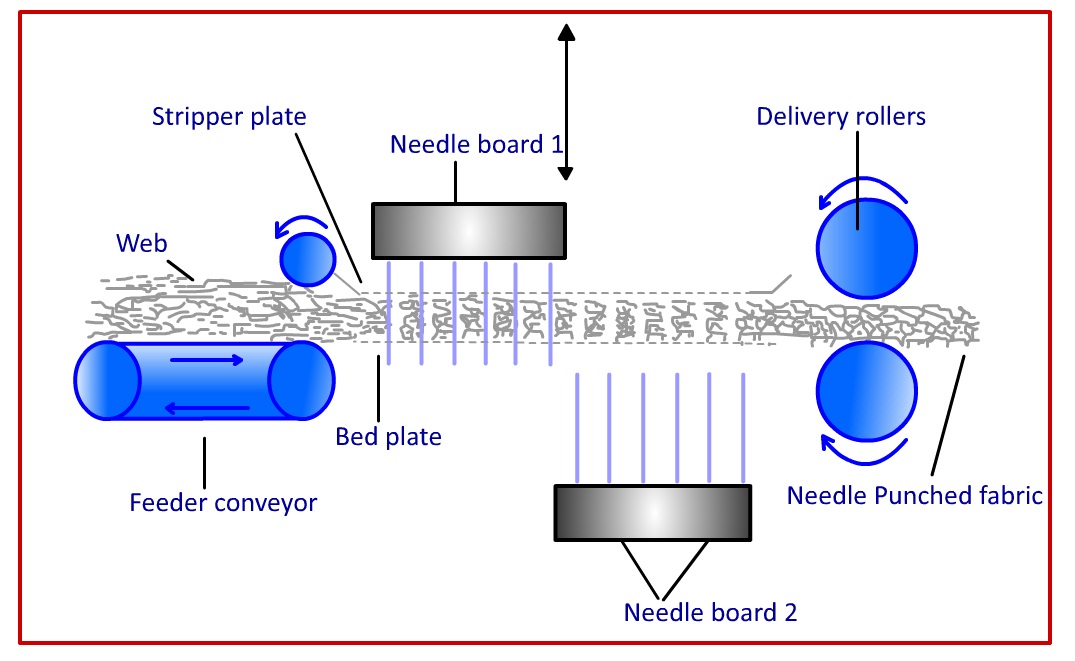 |
Figure 1.21: Needlepunching process |
|
Hydroentanglement Technology
|
Hydroentanglement or spunlacing is a versatile method of bonding the fibrous web using high-pressure water jets. In this process, a fabric is produced by subjecting a web of loose fibres to high-pressure fine water jets as shown in Figure 1.22. The fibre web is supported either by regularly spaced woven wires or surface with randomly distributed holes (Perfojet technology). As a result of the impact of the high pressure jets, the fibres twist around each other, forming an integrated web where fibres are held together by frictional forces. The fabrics are finally dried to remove the water. |
The resulting fabric strength depends on the web properties (basis weight, thickness etc.), fibre parameters (fibre diameter, bending modulus, etc.) and forming wires geometry and jet parameters. Hydroentangled nonwovens have an extensive range of applications like wipes, carpet backing, filters, sanitary, medical dressings and composites. Among these applications, personal care and household wipes form the fastest growing market. Use of natural resources like water and energy (for drying) are some of the concerns for this technology. |
|
Figure 1.22: Hydro-entanglement process
|
|
|
Spunbond and meltblown fabrics belong to the class of polymer-laid nonwovens. In spunbonding process, fluid polymer is converted into finished fabric by a series of continuous operations (Figure 1.23). Polymer is first extruded into filaments and then the filaments are attenuated. While the filaments are being attenuated, they remain under tension. After attenuation, the tension is released and the filaments are forwarded to a surface where the web is formed. The web is then subjected to the bonding process which can be done by chemical and/or thermal process. A binder may be incorporated in the spinning process or applied subsequently (e.g., a latex). Polypropylene and polyester are commonly used for spun-bonding process. Spun-bended nonwovens have high strength but lower flexibility.
|
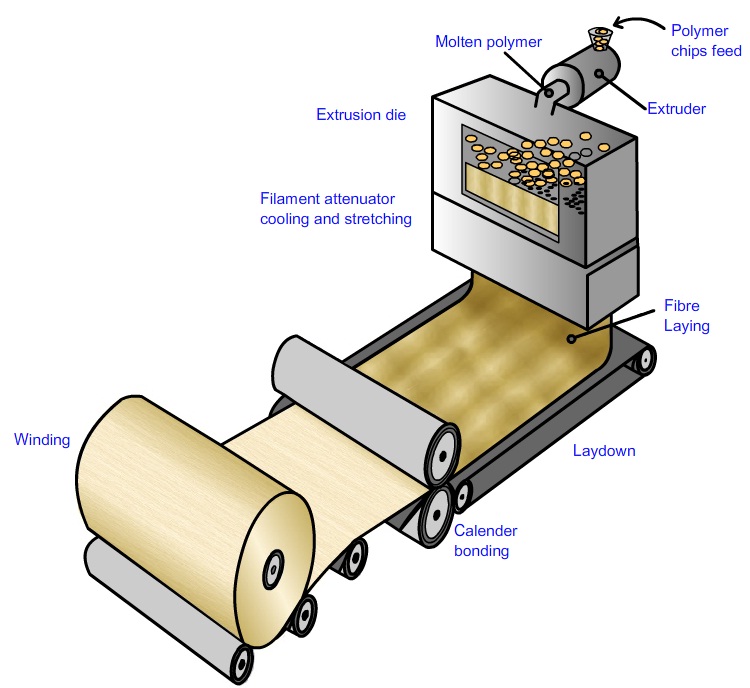 |
Figure 1.23: Spunbonding process |
|
Melt blown technology is unique in the sense that the web is very fine along with very fine pore sizes which no other nonwoven technology can match. The polymer is fed into the die tip and the resulting fibre is attenuated by hot air, which is blown near the die tip as shown in Figure 1.24. Air and fibre are expanded into the free air. Due to the mixture of high speed air and fibre with ambient air, the fibre bundle starts its movement forward and backward creating ‘form drag’. This form drag appears with every change of fibre direction. Therefore the meltblown fibres usually do not have a constant diameter. The fibres in the melt blown web are laid together by a combination of entanglement and cohesive sticking. The ability to form a web directly from a molten polymer without controlled stretching gives melt blown technology a distinct cost advantage over other systems.
|
Melt blown webs offer a wide range of product characteristics such as random Fibre orientation, very fine fibre and low to moderate web strength. The largest end-uses for monolithic melt blown materials are filtration media (surgical mask filters, liquid and gaseous filtration), surgical disposable gown, sterilization wrap, disposable absorbent products, oilsorbents. About 40% of meltblown material is used in the uncombined (monolithic) state. The laminated SMS structures (Spunbond-meltblown-spunbond) are ideal for gradient filtration as the material shows excellent barrier properties combined with mechanical strength. The filtration efficiency often is increased by applying electrostatic loads to the filament to improve filtration efficiency. With this standard meltblown technology fibres with diameter of 1-3 µm can be produced. Several filter applications using meltblown fibres are already in the market today.
|
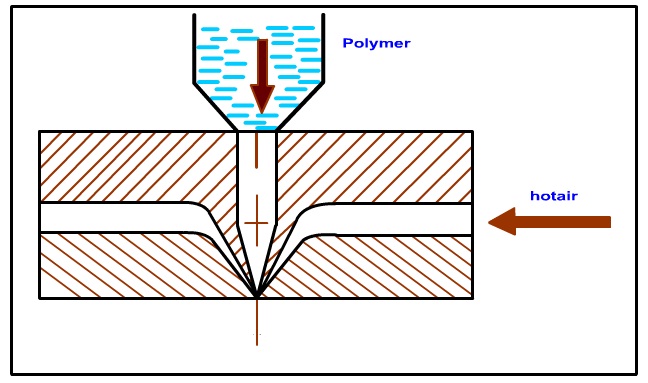 |
 |
Figure 1.24: Schematic diagram of meltblown process
|
|
|
Braiding generally produces tubular or narrow fabrics by intertwining three or more strands yarns, threads or filaments. The yarn packages move on serpentine path as shown in Figure 1.25. In simple machines, half of the packages move in clockwise direction whereas the remaining packages move in anticlockwise direction. Shoelaces and ropes are manufactured using braiding systems. Profiled braided structures are also used as composite performs. The interlacement pattern of braided structure has resemblance with the woven structures. For example, Diamond, Regular and Hercules braids have interlacement patterns similar to those of plain, 2×2 and 3×3 twill weaves respectively. |
|
Figure 1.25: Paths of yarn packages in braiding machine |
During the braiding process, the yarn forms a helical path around a mandrel. The braid angle is defined as the angle between the yarn axis and the braid axis. This is similar to the twist angle of a fibre inside the yarn. The braid angle is very important parameter for the braided structure. It can be calculated using the following expression. |
|
If the number of yarn careers is K then the braided structure forms K/2 number of parallelograms in the circumferential direction. This is shown in Figure 1.26. |
The cover factor for the above braided structure can be calculated using the following expression. |
|
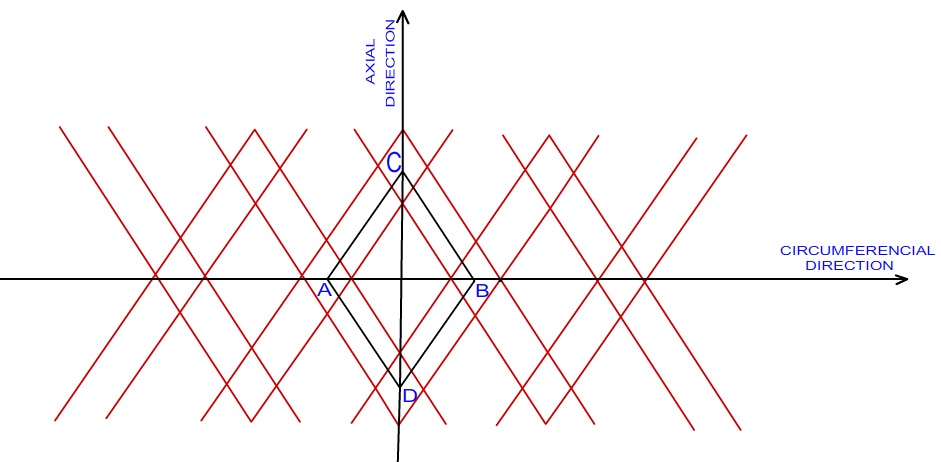
|
Figure 1.26: Unit cell of braided structure |
|
References |
-
Potluri, P., Rawal, A., Rivaldi, M., Porat, I., Geometrical modelling and control of a triaxial braiding machine for producing 3D performs, Composites: Part A 34 (2003) 481–492
|
|
|
|