|
The objective of the course is to introduce the basic concepts of woven fabric manufacturing to the sophomores of Textile Engineering/ Technology. The course material has been designed to create interest among students and hone their analytical ability. |
After attending this course, the students will be able to understand and analyze the preparatory processes of weaving like winding, warping and sizing. They will also be able to analyze various mechanisms of shuttle looms like shedding, picking, beat-up, take-up and let-off. |
More emphasis has been given on the fundamental aspects so that the students get the opportunity to think and learn rather than memorize and learn. All the equations have been derived so that students can understand the contexts better and this has been supplemented with some numerical problems at the end of each module. Some mundane descriptive part which requires memorizing has been deliberately avoided. This pithy course material is not a substitute of standard text books. Students are suggested to read text books for the details. |
Text Books for Further Reading |
- Textile Sizing by B. C. Goswami, R. Anandjiwala and D. M. Hall , Marcel Dekker (2004).
- Textile Mathematics : Volume III by J. E. Booth , The Textile Institute, Manchester.
- Weaving mechanism by R. Marks and A. T. C. Robinson , The Textile Institute, Manchester (1976).
- Weaving: Conversion of Yarn to Fabric by P. R. Lord and M. H. Mohamed , Woodhead Publishing (1999).
- Woven Textiles by K. L. Gandhi, Woodhead Publishing (2012)
|
|
Collaborator: Dr. Anindya Ghosh, Associate Professor, Government College of Engineering and Textile Technology, Berhampore, West Bengal, India ( anindya.textile@gmail.com ) |
|
Acknowledgement: The author extends gratitude to The Textile Institute, Manchester, Sekisui Specialty Chemicals America LLC, Uster Technologis AG, Prashant Group, Ahmedabad, for granting permission to use some figures from their books and technical literature. |
|
Fabric Manufacturing Technologies |
Textile fabrics are generally two dimensional flexible materials made by interlacing of yarns or inter-meshing of loops with the exception of nonwovens and braids. Fabric manufacturing is one of the four major stages (fibre production, yarn manufacturing, fabric manufacturing, and textile chemical processing) of textile value chain. Most of the apparel fabrics are manufactured by weaving technology though knitting is catching up fast specially in the sportswear segment. Natural fibres in general and cotton fibre in particular are the most popular raw material for woven fabrics intended for apparel use. Staple fibres are converted into spun yarns by the use of a series of machines in the yarn manufacturing section. Continuous filament yarns are texturised to impart spun yarn like bulk and appearance to them. |
Textile fabrics are special materials as they are generally light-weight, flexible (easy to bend, shear and twist), moldable, permeable and strong. There are four major technologies of fabric manufacturing as listed below. |
- Weaving
- Knitting
- Non-woven
- Braiding
|
Figure 1.1 depicts the fabrics produced by the four major technologies. |
.jpg) |
.jpg) |
.jpg) |
.jpg) |
Woven |
Knitted |
Nonwoven |
Braided |
|
Figure 1.1: Fabrics produced by different technologies |
Fabric manufacturing may be preceded either by fibre production (in case of nonwoven) or by yarn manufacturing (in case of weaving, knitting and braiding). Fabrics intended for apparel use must fulfill multidimensional quality requirements in terms of drape, handle, crease recovery, tear strength, air permeability, thermal resistance, moisture vapour permeability. However, looking at the unique properties and versatility of textile fabrics, they are now being used in various technical applications where the requirements are altogether different. Some examples are given in Table 1.1.
|
Table 1.1: Properties of some technical fabrics
|
Fabric type |
Important properties/ parameters |
Filter fabric |
Pore size, pore size distribution |
Body armour fabrics |
Impact resistance, areal density, bending resistance |
Fabrics as performs for composite |
Tensile strength and tensile modulus |
Knitted compression bandages |
Stretchability, tensile modulus, creep |
|
|
Weaving is the most popular way of fabric manufacturing. It is primarily done by interlacing two orthogonal sets (warp and weft) of yarns in a regular and recurring pattern. Actual weaving process is preceded by yarn preparation processes namely winding, warping, sizing, drawing and denting. |
Winding converts the smaller ringframe packages to bigger cheeses and cones while removing objectinable yarn faults. Pirn winding is performed to supply the weft yarns in shuttle looms. Figure 1.2 shows various yarn packages used in textile operations (from left to right: ringframe bobbin or cop, cone, cheese and pirn). Warping is done with the objective to prepare a warper’s beam which contains a large number of parallel ends in a double flanged beam. Sizing is the process of applying a protective coating on the warp yarns so that they can withstand repeated stresses, strains and flexing during the weaving process. Finally the fabric is manufactured on looms which perform several operations at proper sequence so that there is interlacement between warp and weft yarns and continuous fabric production. |
|
Figure 1.2: Types of yarn packages |
|
Types of Looms |
Hand Loom: This is mainly used in unorganized sector. Operations like shedding and picking is done by using manual power.This is one of the major sources of employment generation in rural areas. |
|
Power Loom: It was designed by Edmund Cartwright in 1780s (during the industrial revolution). All the operations of the loom are automatic except the change of the pirn. |
|
Automatic Loom: In this power loom, the exhausted pirn is replenished by the full one without stoppages. Under-pick system is a requirement for these looms. |
|
Multiphase Loom: Multiple sheds can be formed simultaneously in this looms and thus productivity can be increased by a great extent. It has failed to gain commercial success. |
|
Shuttle-less Loom: Weft is carried projectiles, rapiers or fluids in case of shuttle-less looms. The rate of production is much higher for these looms. Besides, the quality of the products is also better and the product range much broader compared to that of Power looms. Most of the modern mills are equipped with different types of shuttle-less looms based on the product range. |
|
Circular Loom: Tubular fabrics like hose-pipes and sacks are manufactured by circular looms. |
|
Narrow Loom: These looms are also known as needle looms and used to manufacture narrow width fabrics like tapes, webbings, ribbons and zipper tapes. |
|
Primary Motions |
Figure 1.3 shows some basic components of a loom. For fabric manufacturing through weaving, three primary motions are required namely shedding, picking and beat up. |
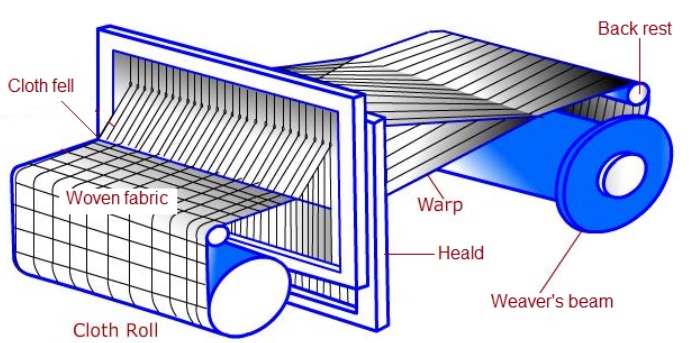 |
Figure 1.3: Basic loom components |
|
Shedding |
It is the process by which the warp sheet is divided into two groups so that a clear passage is created for the weft yarn or weft carrying device to pass through it. One group of yarns (red yarns) either moves in the upward direction or stay in the up position (if they are already in up position) as shown in Figure 1.4. Thus they form the top shed line. Another group of yarns (green yarns) either moves in the downward direction or stay in the down position (if they are already in down position). Thus they form the bottom shed line. |
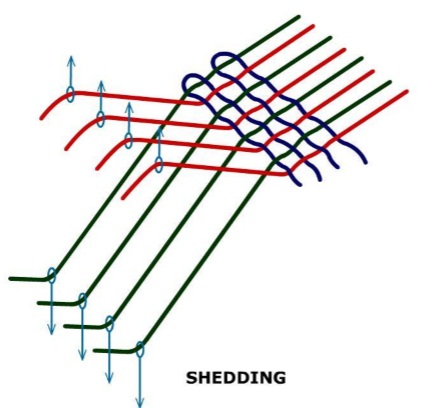 |
Figure 1.4: Shedding |
|
Except for jacquard shedding, warp yarns are not controlled individually during the shedding operation. Healds (Figure 1.5) are used to control a large number of warp yarns. The upward and downward movements of healds are controlled either by cam or dobby shedding mechanisms. The movement of the healds is not continuous. After reaching the top or bottom position, the healds, in general, remain stationary for some duration. This is known as ‘dwell’. In general, the shed changes after every pick i.e. the insertion of weft. |
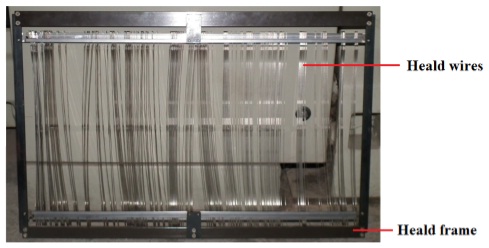 |
Figure 1.5: Heald |
|
Picking |
The insertion of weft or weft carrying device (shuttle, projectile or rapier) through the shed is known as picking. Based on picking system, looms can be classified as follows. |
- Shuttle loom: weft package is carried by the wooden shuttle
- Projectile loom: weft is carried by metallic or composite projectile
- Airjet loom: weft is inserted by jet of compressed air
- Waterjet loom: weft is inserted by water jet
- Rapier loom: weft is inserted by flexible or rigid rapiers
|
Figure 1.6 shows some weft carrying devices. |
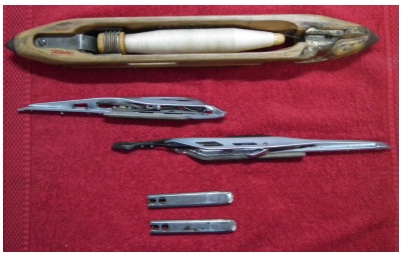 |
Figure 1.6: Shuttle, rapier heads and projectile (from top to bottom) |
|
With the exception of shuttle loom, weft is always inserted from only one side of the loom. The timing of picking is extremely important specially in case of shuttle loom. The shuttle should enter into the shed and leave the shed when the shed is sufficiently open (Figure 1.7). Otherwise, the movement of the shuttle will be obstructed by the warp yarns. As a result, the warp yarns may break due to abrasion or the shuttle may get trapped in the shed which may cause damage to reed, shuttle and warp yarns. |
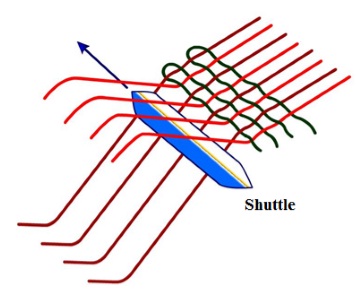 |
Figure 1.7: Picking |
|
Beat-up |
Beat up is the action by which the newly inserted weft yarn is pushed up to the cloth fell (Figure 1.8). Cloth fell is the boundary up to which the fabric has been woven. The loom component responsible for the beat up is called ‘reed’. The reed, which is like a metallic comb, is carried by sley which sways forward and backwards due to the crank-connecting rod mechanism. This is known as crank beat up. In modern looms, beat up is done by cam mechanism which is known as cam beat up. Generally, one beat up is done after the insertion of one pick. |
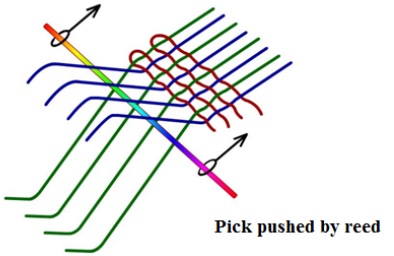 |
Figure 1.8: Beat up |
|
Secondary Motions |
For uninterrupted manufacturing of fabrics, two additional secondary motions are required. These are take-up and let-off. Take-up motion winds the newly formed fabric on the cloth roller either continuously or intermittently after the beat up. The take-up speed also determines the picks/cm value in the fabric at loom state. As the take-up motion winds the newly formed fabric, tension in the warp sheet increases. To compensate this, the weavers beam is rotated by the let-off mechanism so that some new warp sheet is released. |
|
Auxiliary Motions |
Auxiliary motions are mainly related to the activation of stop motions in case of any malfunctioning like warp breakage, weft breakage or shuttle trapping within the shed. The major auxiliary motions are as follows: |
- Warp stop motion (in case of warp breakage)
- Weft stop motion (in case of weft breakage)
- Warp protector motion (in case of shuttle trapping)
|
|
Some Basic Definitions Related to Woven Fabrics |
Yarn count: Yarn count represents the coarseness or fineness of yarns. There are two distinct principles to express the yarn count. |
- Direct systems (Example: Tex, Denier)
- Indirect systems (Example: new English i.e. Ne, Metric i.e. Nm)
|
|
Direct system revolves around expressing the mass of yarn per unit length. In contrast, indirect system expresses length of yarn per unit mass. For example, 10 tex yarn implies that the 1000 m long yarn will have a mass of 10 g. Similarly, for 10 denier, 9000 m long yarn will have a mass of 10 g. Denier is popularly used to express the fineness of synthetic fibres and filaments. A 10 denier yarn is finer than a 10 tex yarn as for the same mass, the length is nine times for the former. |
|
On the other hand, 10 Ne implies that 1 pound yarn will have a length of 10 × 840 yards. As the Ne value increases (say from 10 Ne to 20 Ne), the yarn becomes finer. |
|
Table 1.1 shows the details of some popular yarn count systems. |
Table 1.1: Direct and indirect systems of yarn count |
TYPE |
NAME |
UNIT OF MASS |
UNIT OF LENGTH |
Direct |
Tex |
Gram |
1000 m |
Denier |
Gram |
9000 m |
Indirect |
Ne |
Pound |
Hank (840 yards) |
Metric |
Kilogram |
Kilometer |
|
|
Conversion Factors |
|
Packing factor or packing coefficient: It represents the extent of closeness of fibres within a yarn structure. For the same yarn linear density, if the fibres are closely packed, then its diameter will be less. This happens when a spun yarn is manufactured with high level of twist. Figure 1.9 shows the close packing of circular fibres in a yarn. |
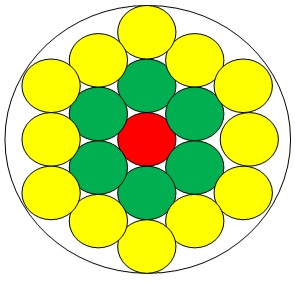 |
Figure 1.9: Close packing of circular fibres |
|
Packing factor is expressed as follows: |
|
|
For spun yarns, the value of packing factor generally lies between 0.55 and 0.65. Yarns with lower packing factor are expected to be more bulky and softer. They can give higher fabric cover for same fabric construction parameters. |
Warp: The group of longitudinal yarns in a woven fabric is called warp. A single warp is called ‘end’. |
Weft: The group of transverse yarns in a woven fabric is called weft. A single weft is called ‘pick’. |
Crimp: It is the measure of the degree of waviness present in the yarns inside a woven fabric due to interlacement. It is expressed as follows: |
 |
Contraction : It is expressed as follows: |
 |
If the warp crimp is 10%, then the straightened length of an end, unraveled from the one meter long fabric, will be 1.1 m. |
|
Fractional cover: It is the ratio of area covered by the yarns to the total area of the fabric. If warp yarn diameter is ‘d1’ inch and spacing between two consecutive ends is ‘p1’ inch then fractional cover for warp (k1) is  |
Now, for cotton yarns, having packing factor of 0.6, the relationship between yarn diameter (inch) and yarn count (Ne) is as follows: |
 |
The relationship between end spacing (p1) and ends per inch (n1) is as follows: |
|
After rearranging, we can write |
|
Cover factor : It is obtained by multiplying fractional cover with 28. |
|
|
Fabric cover is a very important parameter as it influences the following properties of the woven fabrics. |
- Air permeability
- Moisture vapour permeability
- Ultra violet or any other types of radiation protection
|
|
Figure 1.10 shows two fabrics with low and high cover factors |
|
Figure 1.10: Fabrics with low and high cover factors |
|
Areal density : It is expressed by the mass of the fabric per unit area. In most of the cases the mass is expressed in gram (g) and area is expressed in square meter (m2). Therefore, the unit becomes g/m2 which is popularly called as GSM. Areal density of fabric will depend on the following parameters. |
- Warp yarn count
- Weft yarn count
- Ends per unit length (EPI or EPcm)
- Picks per unit length (PPI or PPcm)
- Crimp% in warp
- Crimp% in weft
|
|
|
|
|
|