Wind turbine blade application
Ghoshal [2000] has performed structural health monitoring testing on a full wind turbine blade during loading using the stress wave propagation technique. The health monitoring experiments are performed while the wind turbine blade is being quasi-statically loaded to failure. Bonded piezo-ceramic patches are used for generating and receiving the stress waves. The raw signals received from sensors in the vicinity of the final failure (rifer to Figure 10.1) have shown recognizable changes in stress wave parameters. These changes have occurred well ahead of the final failure. The stress wave data are processed using three different damage detection and signal processing algorithms based on wavelet transformation. All algorithms have indicated a change in the structure with loading. These results could be used for early detection of damage and to possibly provide guidelines for design of the blade.
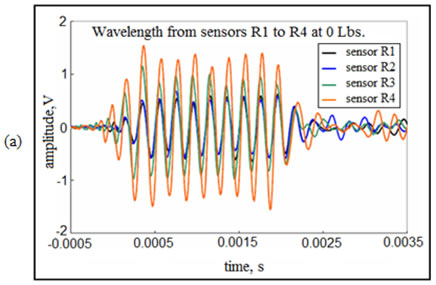
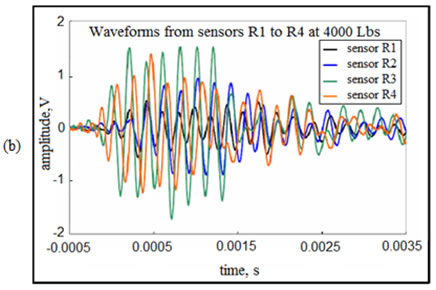
Figure 10.1 Comparisons of waveforms from sensors at (a) No load condition and
(b) At a load of 4000-4500 lb [Ghoshal, 2000].
|