Gas Turbine System , Centrifugal and Axial Flow Compressors
Introduction
A turbofan engine that gives propulsive power to an aircraft is shown in Figure 4.1 and the schematic of the engine is illustrated in Figure 4.2. The main components of the engine are intake, fan, compressor, combustion chamber or burnner, turbine and exhaust nozzle.
The intake is a critical part of the aircraft engine that ensures an uniform pressure and velocity at the entry to the compressor. At normal forward speed of the aircraft, the intake performs as a diffusor with rise of static pressure at the cost of kinetic energy of fluid, referred as the 'ram pressure rise'. Then the air is passed through the compressor and the high pressure air is fed to the combustion chamber, where the combustion occurs at more or less constant pressure that increases its temperature. After that the high pressure and high temperature gas is expanded through the turbine. In case of aircraft engine, the expansion in the turbine is not complete. Here the turbine work is sufficient to drive the compressor. The rest of the pressure is then expanded through the nozzle that produce the require thrust.
However, in case of stationery gas turbine unit, the gas is completely expanded in the turbine. In turbofan engine the air is bypassed that has a great effect on the engine performance, which will be discussed later. Although each component have its own performance characteristics, the overall engine operates on a thermodynamic cycle.
Figure 4.1 Gas Turbine (Courtesy : ae.gatech.edu) |
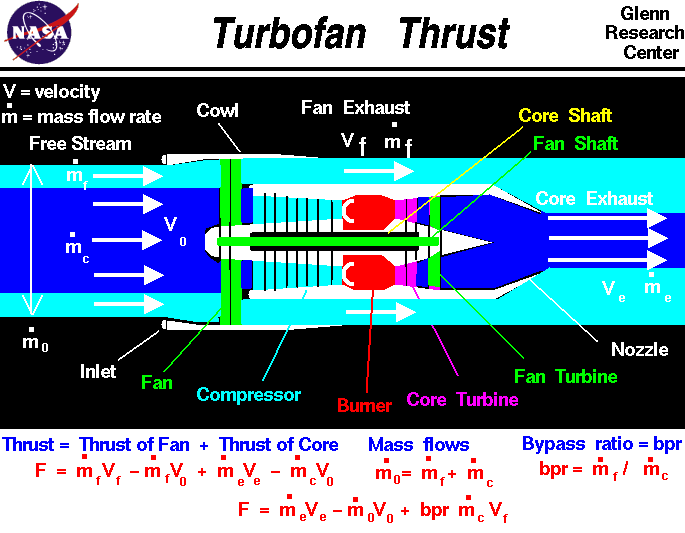
Figure 4.2 (Courtesy : NASA Glenn Research Centre) |
In this chapter, we will describe the ideal gas turbine or aircraft propulsion cycles that are useful to review the performance of ideal machines in which perfection of the individual component is assumed. The specific work output and the cycle efficiency then depend only on the pressure ratio and maximum cycle temperature. Thus, this cycle analysis are very useful to find the upper limit of performance of individual components.
Following assumptions are made to analysis an ideal gas turbine cycle.
(a) The working fluid is a perfect gas with constant specific heat.
(b) Compression and expansion process are reversible and adiabatic, i.e isentropic.
(c) There are no pressure losses in the inlet duct, combustion chamber, heat exchanger, intercooler, exhaust duct and the ducts connecting the components.
(d) The mass flow is constant throughout the cycle.
(e) The change of kinetic energy of the working fluid between the inlet and outlet of each component is negligible.
(f) The heat-exchanger, if such a component is used, is perfect.
|