|
Balancing Machines
Various types of balancing machines are commercially available. These are
commonly used in the production line of rotors. There are two common balancing machines:
- For low-speed, rough rotors which do not require a very high degree
of balancing - pivoted-carriage machines are used.
- For intermediate-speed, smooth rotors which need a comparatively more accurate balancing - Gisholt-type balancing machines are used.
Pivoted-Carriage Balancing Machine
The rotor to be balanced is mounted on half-bearings in a light but stiff carriage
(Fig. 5.1). This carriage is pivoted near one end and rests on a spring at the
other.
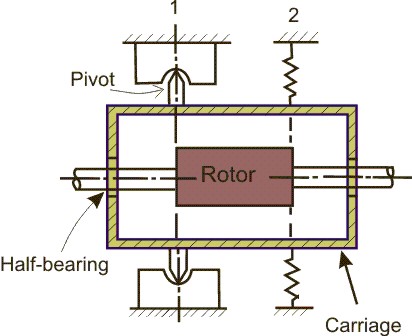
Fig. 5.1: Rotor mounted in half-bearings
-
The rotor is mounted with plane 1 coinciding with
the pivot axis so that the unbalance in this plane has no effect on the carriage
motion. When the rotor is rotated in this position, the carriage oscillates due
only to the unbalance in plane 2.
-
A trial mass is then placed (at a known radius)
in plane 2 and the amplitude of carriage oscillation is noted.
-
The procedure is
repeated with the same trial mass (at the same radius) at different angular
positions. A plot of the observed amplitude of carriage motion against the
angular position of the trial mass indicates the best angular position for which
the amplitude is minimum.
-
The magnitude of the trial mass is varied at this
angular position, and the exact amount of balance mass, which reduces the
amplitude to almost zero, is determined by trial and error.
-
A similar procedure
is followed to determine the required balancing mass in plane 1, the rotor being
mounted with plane 2 coinciding with the pivot axis.
Congratulations! You have finished Lecture 5.
|