|
- Pultrusion:
It is a continuous process in which composites in the form of fibers and fabrics are pulled through a bath of liquid resin. Then the fibres wetted with resin are pulled through a heated die. The die plays important roles like completing the impregnation and controlling the resin. Further, the material is cured to its final shape. The die shape used in this process is nothing the replica of the final product. Finally, the finished product is cut to length.
In this process, the fabrics may also be introduced into the die. The fabrics provide a fibre direction other 0°. Further, a variant of this method to produce a profile with some variation in the cross-section is available. This is known as pulforming.
The resins like epoxy, polyester, vinylester and phenolic can be used with any fibre.
The pultrusion process is shown in Figure 1.18.
Advantages:
- The process is suitable for mass production.
- The process is fast and economic.
- Resin content can be accurately controlled.
- Fibre cost is minimized as it can be taken directly from a creel.
- The surface finish of the product is good.
- Structural properties of product can be very good as the profiles have very straight fibres.
Disadvantages:
- Limited to constant or near constant cross-section components.
- Heated die costs can be high.
- Products with small cross-sections alone can be fabricated.
Applications:
Beams and girders used in roof structures, bridges, ladders, frameworks
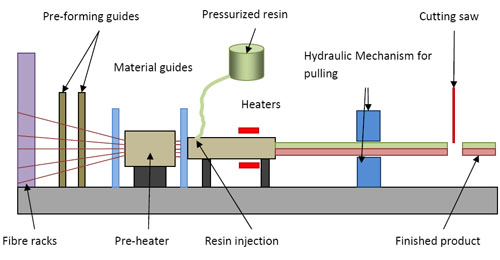 |
|
|
|
|
|
|
|
|
|
|
|
|
|
|
|
|
|
|
|